VALVE STEM SEALS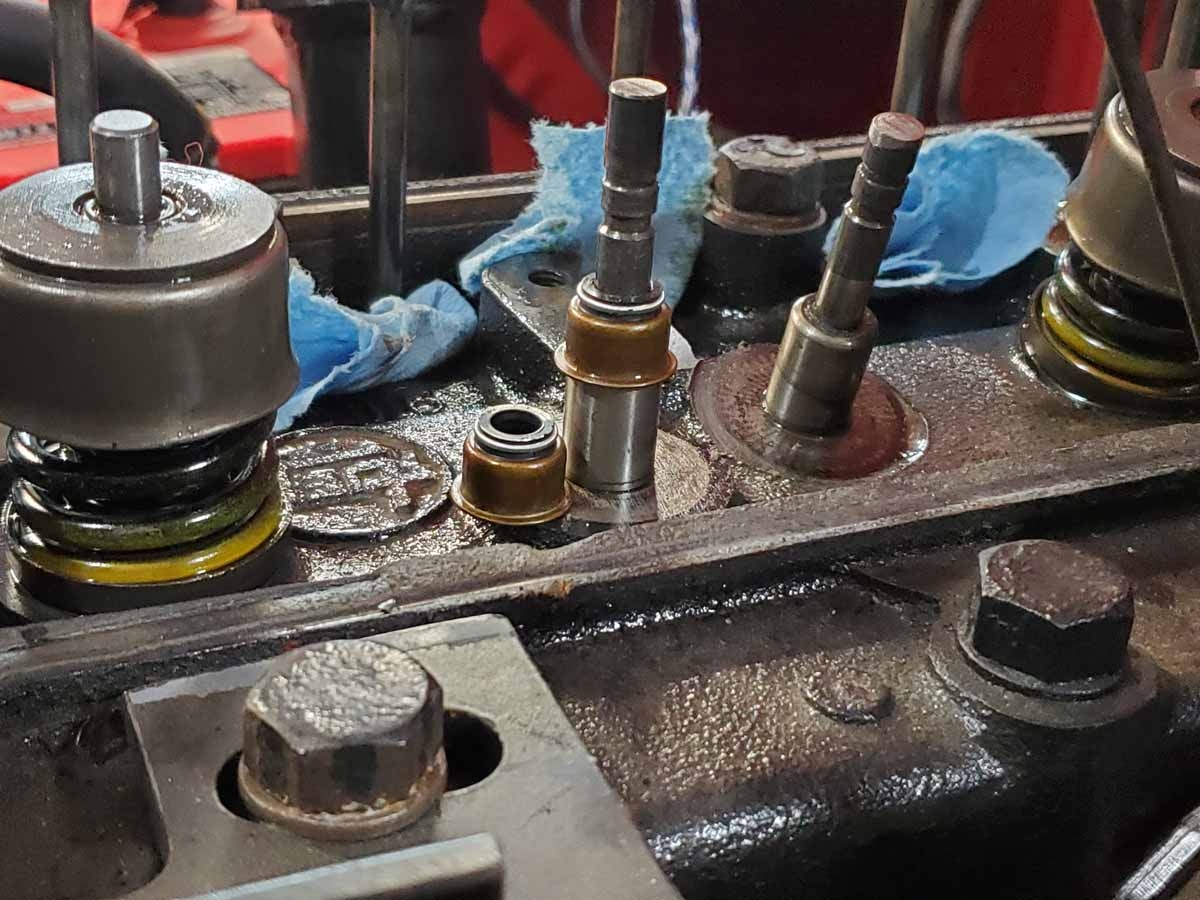
CDI engineers analyze the OE design for every application. The OE design is tested and benchmarked. Based on the analysis, we determine the material used, considering the durometer (relative hardness) of the rubber, temperature requirements (both extreme heat and extreme cold), resistance to common oil types, tear-resistance and leak rate.
This type of analysis makes one thing clear, not all valve stem seals are created equal. Visually, a lower-quality seal may look very similar to a high-quality seal that’s appropriate for a given engine platform. However, a lower-quality seal with insufficient heat-resistance will harden and crack prematurely and will not work as intended.
You can count on CDI to use the right material for each application. CDI uses a variety of materials including nylon, PTFE, rubber, steel and synthetic rubber or some combination of these. FKM, fluoroelastomer, is used in many CDI valve stem seals for hotter-running, late-model vehicles. It is often combined with a metal jacket or covering that totally surrounds the FKM positive seal. FKM offers excellent resistance to both heat (up to 450°F) and abrasion.
How does the valve work?
Valve seals work by forming a tight barrier between moving elements, typically the valve stem and the valve guide. As the valve opens and shuts several times during operation, its seal must retain integrity under various pressures, temperatures, and mechanical motions. This is accomplished by precise engineering of both material composition and geometric design of the seal.
These seals are made of rubber, polytetrafluoroethylene (PTFE), and other polymers that are resistant to wear and chemical damage. The material used is determined by the individual application requirements, such as temperature resistance, compatibility with the fluids or gasses to be sealed, and durability.
In terms of design, most valve seals include a lip structure that securely wraps around the valve stem. This lip is designed to impart just enough pressure to the stem to form a seal while minimizing friction, which may otherwise cause premature wear or damage to either component. Some designs additionally use springs or other mechanical mechanisms to maintain continuous pressure around the stem regardless of the circumstances.
As valves are actuated (opened or closed), the seal must adjust dynamically to pressure fluctuations while maintaining its sealing qualities. This flexibility avoids leakage, which might jeopardize system efficiency or safety. Furthermore, by avoiding direct metal-to-metal contact between moving components through appropriate sealing procedures, wear over time is reduced, hence increasing total component lifespan.
What are the types of valves?
Positive Valve Seals:They are made of high-grade rubber or synthetic materials and are designed to fit tightly around the valve stem. They are used in engines to reduce oil consumption and keep oil from entering the combustion chamber. Positive seals are direct-contact seals that fit securely against the valve stem and provide perfect control over oil flow.
Deflector Valve Seals: Also called as umbrella seals, these are constructed of rubber or silicone and are intended to deflect oil away from the valve stem. They do not create as tight a seal as positive valve seals, but they are useful in older engines with less accurate oil management requirements. Deflector seals capture oil that drops down from the valve guide and divert it away from the stem.
What will happen if the valve oil seal is broken?
When the valve oil seal ages, it becomes loose and cannot effectively seal the valve, resulting in valve leakage. This makes the engine less fuel efficient, reduces the engine's power output, and reduces the car's ability to accelerate. At the same time, the aging of valve oil seal will also increase the emission of pollutants, causing pollution to the environment.
It will also cause the engine power decline and fuel consumption to increase significantly, and the related parts are damaged, especially the spark plug condition has decreased significantly. The valve oil seal has two main functions, one is to prevent the mixture of gasoline and air and the leakage of exhaust gas, and the other is to prevent the engine oil from entering the combustion chamber.
Finally, due to the valve oil seal damage, the oil will enter the cylinder to participate in combustion, resulting in carbon deposits, carbon deposits in the oil will make the engine lubrication worse, increase engine wear. Valve seal accessories introduction: valve rod seal is a kind of oil seal, generally by the outer frame and fluorine rubber vulcanization.
The symptom of automobile valve oil seal failure is oil leakage; The leakage of valve seal will accelerate the loss of oil; Blue smoke comes from the rear exhaust pipe. This causes oil to leak into the cylinder, forming a "burning oil" phenomenon. Determine the valve oil seal damage method is as follows: remove the intake manifold, you can find a black gelatinous substance on the top of the valve.
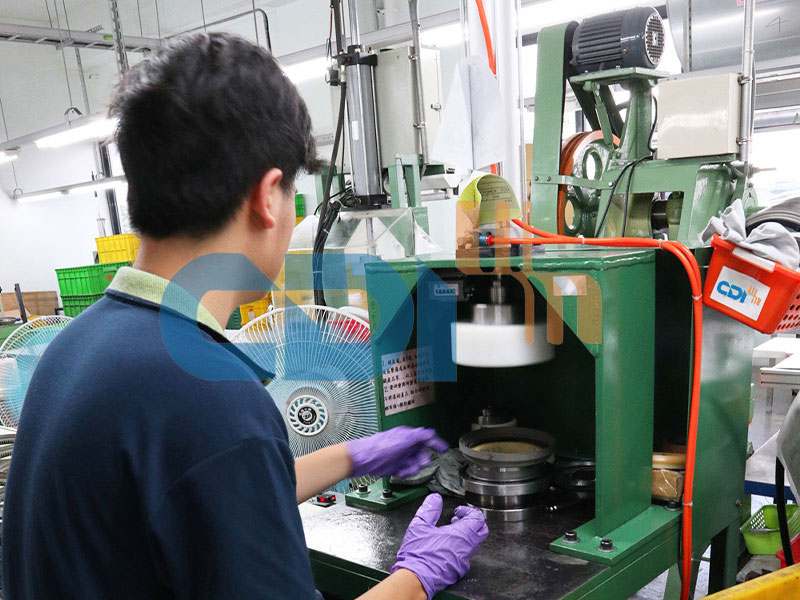
These signs indicate that your valve oil seal should be replacedOur team pay
1. Conducting a Cold Engine Test
One of the best ways to tell if you have a faulty valve seal is to conduct a cold engine test. After your machine hasn’t run for a while — even overnight — the seal is now cool. Once you start the engine, the seal will contract. Damaged seals will leave a small gap. Leftover oil will then settle at the top of the valve cover head.
2. Increased Smoke Levels
Depending on the machines and equipment you use, smoke is often a common form of exhaust. However, when you start seeing it last longer than usual or appear a different color, you know a faulty seal may be the cause. The excessive smoke may also come in more consistent waves as the engine runs for long periods. Be aware of specific machine movements that cause more smoke than usual.
3. More Oil Consumption
If you notice you’re going through more oil than usual, it can be another indication of a bad seal. When oil leaks or burns at higher rates, the seal no longer controls the oil flow. Burning oil increases emissions and can contaminate the catalyst. Unburned fuel in the exhaust skyrockets the converter’s operating temperatures, which can cause the converter to overheat and create a blocked exhaust.